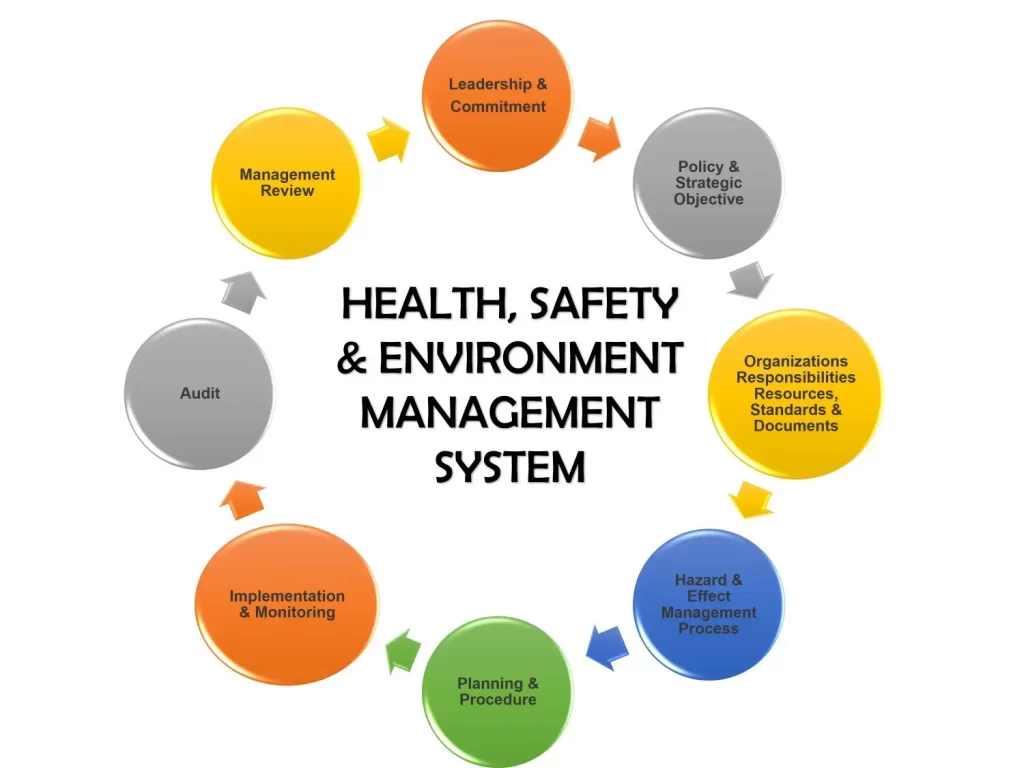
The greatest Safety and Health Management Systems (S&HMS) integrate employees at all levels of the organisation, fostering a safety culture that decreases workplace accidents and boosts organisational profits. Everyone benefits when safety and health are integrated into the organisation as a culture. A Safety and Health Management System (SHMS) is a method for managing workplace safety and health in a systematic manner. Setting goals, planning, monitoring performance, managing commitments and direction are all part of this process. Green Tech S&HMS experts help companies build and execute effective safety and health management systems to ensure that their company follows acceptable WSH practices.
Safety and Health Management System Implementation Criteria
The development of a Safety and Health Management System is required for the following workplaces:
A construction site or a shipyard – A factory producing manufactured metal items, machinery, or equipment (with more than 100 employees). A semiconductor wafer production facility. A facility that processes petroleum or petrochemical products, as well as their intermediates. Premises with a storage capacity of 5,000 cubic metres or more where dangerous or combustible liquids are transported in bulk for the purpose of commerce or profit. Any plant that produces fluorine, chlorine, hydrogen fluoride, or carbon monoxide, as well as synthetic polymers.
Understand the important parts of an efficient safety and health management system at your company before hiring GreenTech consultants. Green Tech services focus on S&HMS implementation on 4 aspects or levels in an organisation as follows:
A. Employee Engagement and Management Commitment
Create a safety and health policy for all employees and make it known to them. Instil accountability for safety and health, follow safety standards, and evaluate accident records to demonstrate management commitment. Hold regular meetings with employees, managers, and supervisors to discuss safety and health. Assign a person or people to be in charge of coordinating safety and health activities. Make safety and health a priority in your firm (e.g., purchases, contracts, design and development) Employees should be involved in safety and health-related activities (e.g., self-inspections, accident investigations and developing safe practices) Employees should be praised for their safe and healthy work habits.
B. Worksite Analysis
Hazards should be assessed in all work activities and procedures. Whenever procedures, materials, or machinery change, re-evaluate workplace operations. Conduct on-site inspections, identify potential dangers and implement corrective measures. Employees should be able to report hazardous or unhealthy circumstances using a hazard reporting system. To establish the fundamental causes of all accidents and near misses, conduct an investigation.
C. Hazard Prevention and Control
Workplace dangers must be eliminated and controlled (e.g., engineering controls, workstation design and work practises) Create a preventative maintenance plan. Keep employees informed about actions and situations that affect their safety and health. Prepare for the unexpected (e.g., create an evacuation plan, train employees and conduct fire drills) Keep track of and analyse workplace injuries and illnesses.
D. Training For Employees, Supervisors and Managers
Before an individual starts work, provide instruction on specific safe work practices. Additional training should be provided for new work processes as well as when accidents or near misses occurred. Refresher training should be conducted within a specific time period.
The 4 tier service portfolio mentioned above from Green Tech Singapore helps organisations in the development of safety and health management systems more efficiently and cost-effectively.
Workplace Safety and Health Audit
Certain workplaces are required to audit their SHMS regularly to ensure that the system stays stable. If your workplace is one of the following, you must appoint a SAC-accredited WSH Auditing Organisation or a MOM-approved WSH auditor to audit your SHMS:
Any job site with a contract worth more than $30 million should conduct an audit at least once every six months. Any shipyard with a workforce of 200 or more persons or any plant that employs 100 or more people and manufactures fabricated metal items, machinery or equipment should conduct an audit once every 12 months. Any facility that processes or manufactures petroleum, petroleum products, petrochemicals or petrochemical products should conduct an audit at least once every 24 months. Any facility with a storage capacity of 5,000 cubic metres or more that stores hazardous or flammable liquids should conduct an audit at least once every 24 months. Fluorine, chlorine, hydrogen fluoride, carbon monoxide and synthetic polymers manufacturing factories should conduct an audit at least once every 24 months. Any facility that produces pharmaceuticals or their intermediates should conduct an audit at least once every 24 months. Any semiconductor wafer production facility should conduct an audit at least once every 24 months.
Internal SHMS Review
If your company falls into one of the following categories, you’ll need to undertake an internal evaluation of the SHMS regularly:
Any project with a contract value of less than $30 million should conduct an internal review at least once every 6 months. Any shipyard with fewer than 200 employees should conduct an internal review at least once every 12 months.
An internal evaluation of your SHMS, like a WSH audit, should be performed by a SAC-accredited WSH Auditing Organisation or a MOM-approved WSH auditor.
Governing Laws and Industry Standards
As an employer, you must follow Singapore’s WSH regulations. You should pay special attention to the following:
WSH Regulations (Safety and Health Management System and Auditing) Regulations on
Workplace Safety and Health
(Risk Management)
You should also follow industry best practices, such as:
SS ISO 45001: Occupational Health and Safety Management Systems SS 651: Chemical industry Safety and Health Management System CP 79: Code of Practice for Construction Worksite Safety Management Systems
Green Tech’s highly experienced team of Quality, Environmental, Safety and Health consultants are here to assist you in achieving any management system standards which are required in your esteemed organisation. With our vast knowledge and experiences in various industries, you can always count on us to take you through this journey.